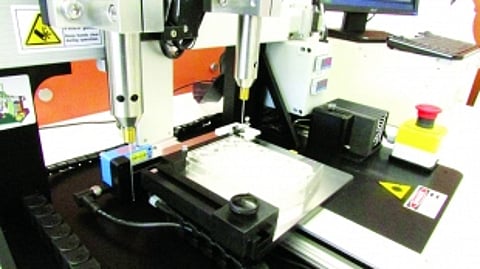
3D printing or additive manufacturing is a process of making three-dimensional solid objects from a digital file. The creation of a 3D printed object is achieved using additive processes. In an additive process, an object is created by laying down successive layers of material until the object is fashioned. Each of these layers can be seen as a thinly sliced cross-section of the object. 3D printing is the opposite of subtractive manufacturing which is hollowing out a piece of metal or plastic with, for instance, a milling machine.
3D printing enables you to produce complex shapes using less material than traditional manufacturing methods. The three-dimensional printing technology was originally developed for non-biologic applications by its inventor Charles Hull, who patented a method in which sequentially printed layers of a material that could be cured with UV light served to build a three-dimensional structure. Researchers estimate that 3D bio-printing can be used to reconstruct tissue from various regions of the body. Patients with end-stage bladder disease, for instance, can be treated by using engineered bladder tissues to rebuild the damaged organ. This technology can also potentially be applied to bone, skin, cartilage and muscle tissue. 3D bio-printing in the future will be used for medical applications in clinical settings – 3D printed skin grafts, bone grafts, implants and biomedical devices.
Bio-printing is combination of 3D printing with bio-materials to replicate parts that imitate natural tissues, bones, and blood vessels in the body. Generally, an artificial organ is an engineered device that can be implanted or integrated into a human body—interfacing with living tissue—to replace a natural organ, to duplicate or augment a specific function or functions so the patient may return to a normal life as soon as possible.
In a breakthrough discovery, researchers at Lund University, Sweden, have recently designed a new “bioink” which allows small human-sized airways to be 3D-bioprinted with the help of patient cells for the first time. The 3D-printed constructs are biocompatible and support new blood vessel growth into the transplanted material. This is an important first step towards 3D-printing organs. The 3D-printed constructs are biocompatible and support new blood vessel growth into the transplanted material.
For many chronic diseases there is no cure and the only end-stage option for patients is lung transplantation. However, there are not enough donor lungs to meet clinical demand. Therefore, researchers are looking at ways to increase the amount of lungs available for transplantation. One approach is fabricating lungs in the lab by combining cells with a bioengineered scaffold.
Researchers first designed a new bio-ink (a printable material with cells) for 3D-bioprinting human tissue. The bio-ink was made by combining materials: a material derived from seaweed, alginate, and extracellular matrix derived from lung tissue. This new bio-ink supports the bio-printed material over several stages of its development towards tissue. Bio-ink is then used to 3D-bio-print small human airways containing two types of cells found in human airways. However, this bio-ink can be adapted for any tissue or organ type.
"These next generation bio-inks also support the maturation of the airway stem cells into multiple cell types found in adult human airways, which means that less cell types need to be printed, simplifying the numbers needed to print tissue made of multiple cell types," says Darcy Wagner, Senior Lecturer, Wallenberg Molecular Medicine Fellow. Wagner notes that the resolution needs to be improved to 3D-bio-print more distal lung tissue and the air sacks, known as alveoli that are vital for gas exchange. The new study has been published in “Advanced Materials”, but we still have a long way to go. The team used a mouse model closely resembling the immune-suppression used in patients undergoing organ transplantation. When transplanted, they found that 3D-printed constructs made from the new bio-ink were well-tolerated and supported new blood vessels.
Bio-printing is an emerging technology with various applications in making functional tissue constructs to replace injured or diseased tissues. It is a relatively new approach that provides high reproducibility and precise control over the fabricated constructs in an automated manner. During the bio-printing process, a solution of a biomaterial or a mixture of several biomaterials in the hydrogel form, usually encapsulating the desired cell types, termed the “bioink”, is used for creating tissue constructs. This “bio-ink” can be cross-linked or stabilized during or immediately after bio-printing to generate the final shape, structure, and architecture of the designed construct. “Bio-inks” may be made from natural or synthetic biomaterials, or a combination of the two as hybrid materials. An ideal “bio-ink” should possess proper mechanical, rheological, and biological properties of the target tissues, which are essential to ensure correct functionality of the bio-printed tissues and organs.
The ultimate goal now is to reproduce a human heart that could be transplanted into patients. A team of researchers from Tel-Aviv University successfully 3D printed a heart using human cells back in April 2019. Researchers estimate that it will take an additional 10 to 15 years before this solution is viable.
It is pretty sure that as days go by we will see fantastic developments in this direction - veritable medical miracles in an unfolding horizon.
(Dr Francisco Colaço is a seniormost consulting physician, pioneer of Echocardiography in Goa)